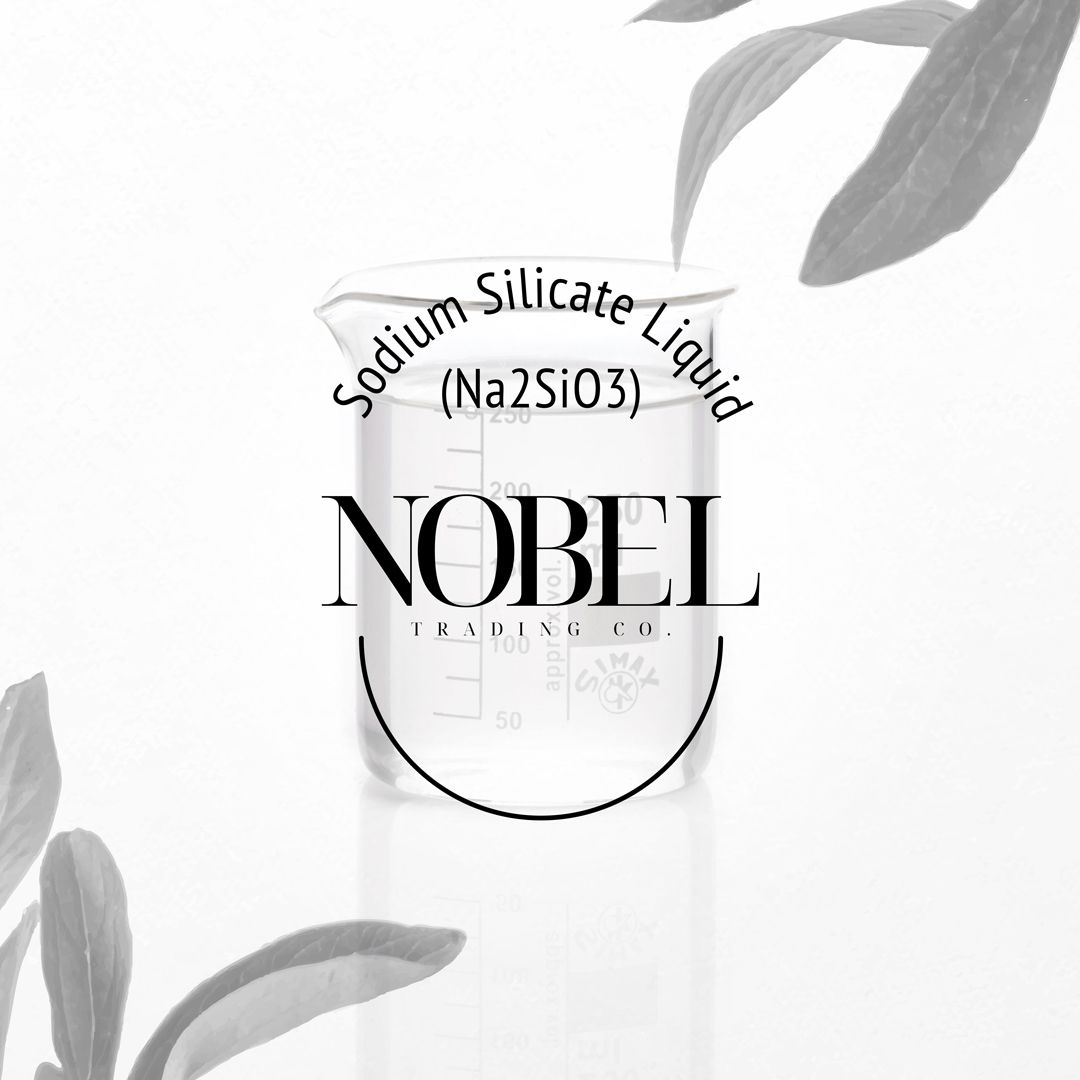
Sodium Silicate Powder & Liquid (Na2SiO3)
Sodium silicate, commonly referred to as water glass or liquid glass, is an inorganic compound with a wide range of useful properties. Its general formula, Na₂O·nSiO₂, indicates a ratio between silicon dioxide (SiO₂) and sodium oxide (Na₂O), which can vary and result in different grades with distinct properties. This compound is known for its adhesive, detergent, and emulsifying characteristics, making it valuable in a wide range of industries, including construction, water treatment, detergents, and ceramics. In this article, we will take a closer look at sodium silicate, exploring its definition, different grades, production process, and varied applications.
Nobel Trading Co is a trusted supplier of both sodium silicate powder and liquid. The company is known for its commitment to delivering high-quality products that meet various industrial needs. With advanced manufacturing facilities, a team of experienced professionals, and strong partnerships with global raw material suppliers, Nobel Trading Co ensures a consistent supply of sodium silicate at competitive prices. The company also offers flexible packaging options, reliable logistics support, and excellent customer service, making it a dependable choice for industries seeking a steady and quality source of sodium silicate.
What is Sodium Silicate?
Sodium silicate, commonly referred to as water glass or liquid glass, is an inorganic compound with the general formula Na₂O·nSiO₂. In this formula, ‘n’ represents the ratio of silicon dioxide (SiO₂) to sodium oxide (Na₂O), which can vary, leading to different types of sodium silicate with distinct properties. This compound is used in many industries, known for its adhesive, detergent, and emulsifying characteristics.
Physical Properties
Sodium silicate can appear in different forms, including a colorless to slightly hazy solid or as a white powder. In liquid form, it is typically a clear or slightly opalescent viscous solution. The density of the solid form is around 2.4 g/mL at 25°C, though this value can vary depending on the SiO₂:Na₂O ratio and hydration level. The melting point for sodium metasilicate (Na₂SiO₃) is approximately 1,088°C (1,990°F), though it may differ based on the specific composition. Sodium silicate does not boil but instead decomposes at high temperatures, and it remains stable up to high heat, making it suitable for various high-temperature uses.
Sodium silicate is highly soluble in water, forming an alkaline solution, but its solubility decreases as the SiO₂ content increases. The compound is insoluble in organic solvents. It has a refractive index of around 1.42, which can vary slightly depending on the concentration and composition.
Chemical Properties
Sodium silicate has the general chemical formula Na₂O·nSiO₂, with sodium metasilicate (Na₂SiO₃) being one common form. The molecular weight depends on the specific compound; sodium metasilicate is 122.06 g/mol. Sodium silicate solutions are typically highly alkaline, with a pH ranging from 11 to 13 for a 1% solution at 20°C. The compound is stable in neutral and alkaline environments but hydrolysis in acidic conditions, forming silicic acid that can polymerize into a gel-like substance.
In terms of reactivity, sodium silicate reacts with acids to produce gelatinous silica (silicic acid) and the sodium salts of the acid used. For example:
Na₂SiO₃ + 2HCl → H₂SiO₃ (↓) + 2NaCl
Additionally, sodium silicate gradually reacts with carbon dioxide in the air to produce silica gel and sodium carbonate:
Na₂SiO₃ + CO₂ → Na₂CO₃ + SiO₂ (↓)
Sodium silicate also exhibits excellent heat resistance, capable of withstanding temperatures up to 1,100°C, which makes it suitable for use in refractory applications. In aqueous solutions, it undergoes partial hydrolysis, contributing to the high alkalinity and pH of the solution.
Different Grades of Sodium Silicate
Sodium silicate is available in various grades that differ based on their SiO₂:Na₂O ratio, physical form, concentration, and other properties like reactivity and solubility. Understanding these differences helps select the most suitable grade for specific industrial applications. Below is an overview of the key grades of sodium silicate.
Alkaline Grades
Alkaline grades of sodium silicate have a SiO₂:Na₂O ratio typically below 2.85:1, ranging from approximately 1:1 to 2.5:1. These grades contain a higher sodium oxide content, which increases their alkalinity and reactivity. They also have greater solubility, meaning they dissolve readily in water, and their lower viscosity makes them easier to handle in liquid form.
Their application in detergents and cleaning agents enhances cleaning effectiveness and softens hard water. Additionally, they find use in adhesives and binders, particularly for paper, cardboard, and wood, due to their strong bonding properties. In water treatment, these grades function effectively as flocculants and corrosion inhibitors, while in the textile industry, they stabilize bleaching and dyeing processes.
Neutral Grades
Neutral grades of sodium silicate have a SiO₂:Na₂O ratio typically above 2.85:1, ranging from about 2.5:1 to 3.5:1. These grades offer a balanced composition with moderate alkalinity and reactivity, making them versatile for various applications. They provide improved chemical stability compared to alkaline grades and have moderate viscosity, suitable for processes that require thicker solutions.
Neutral grades function as binders in refractory materials, enhancing strength and heat resistance. They are also incorporated into fire-resistant coatings for passive fire protection and are utilized as deflocculants in ceramics and foundry applications. In construction materials, their role in cements, mortars, and sealants enhances both durability and bonding.
Liquid Grades
Liquid grades of sodium silicate are available as aqueous solutions with concentrations typically ranging from 35% to 40% solids, though concentrations can be adjusted to meet specific requirements. These grades offer convenient handling as ready-to-use solutions, eliminating the need for additional dissolution steps. The viscosity of liquid grades can be adjusted by modifying the concentration or temperature, making them adaptable for different uses.
Liquid grades serve as an effective sealant in automotive repair, particularly for radiators and engine blocks, forming a glass-like barrier to prevent leaks. In concrete applications, they penetrate and seal surfaces to protect against moisture and chemical exposure. They are also integrated into liquid adhesive formulations for paper, cardboard, and wood products.
Solid Grades
Solid grades of sodium silicate are available in powder, granular, or prill forms, which are small, bead-like pellets. These grades have a long shelf life, making them stable for extended storage periods without degradation. Solids are also more compact and easier to handle compared to liquid forms, facilitating transport and storage.
Solid grades are integral to detergent manufacturing, acting as a raw material for powdered detergents and cleaning agents. In ceramic production, they function as a dry binder in ceramic bodies and glazes. Additionally, solid grades are well-suited for industrial processes requiring dry ingredients or precise dosing.
Siliceous (Acidic) Grades
Siliceous grades of sodium silicate have a SiO₂:Na₂O ratio typically above 3.5:1. These grades contain a higher silica content, resulting in lower alkalinity and reduced solubility in water. They tend to form viscous or gel-like solutions and offer enhanced chemical stability, making them suitable for applications requiring minimal reactivity.
Siliceous grades act as specialized binders in applications that benefit from high silica content, including specific coatings and sealants. They also serve as a source of silica in chemical synthesis processes and are incorporated into coatings requiring high SiO₂ content for enhanced durability.
Sodium Silicate Production Process
The production of sodium silicate can be accomplished through various methods, with the wet process being one of the primary approaches. This method directly reacts caustic soda (sodium hydroxide) with silica sand under high temperature and pressure. The wet process is efficient for producing sodium silicate solution without requiring melting steps, making it an energy-conserving option. In the following, you can read details about the wet method of making sodium silicate.
Raw Materials
Silica sand (SiO₂), which is a fine, high-purity quartz sand, and sodium hydroxide (NaOH), commonly known as caustic soda, are the two key raw materials used. Silica sand provides the necessary silica, which plays a vital role in forming the silicate structure, while sodium hydroxide acts as the alkali reagent that facilitates the reaction. The purity of silica sand is crucial, as impurities can affect the efficiency of the reaction and the quality of the final product. Similarly, the sodium hydroxide must be of high purity to prevent unwanted by-products. Both raw materials are carefully sourced and prepared to ensure they meet the necessary specifications for effective production.
Preparation of Raw Materials
The silica sand is ground to increase its surface area, which significantly enhances the reactivity by allowing more contact points between the sand and the sodium hydroxide. This grinding process is critical as it directly affects the rate and efficiency of the subsequent chemical reaction. After grinding, the sodium hydroxide and silica sand are carefully weighed and thoroughly mixed according to the desired molar ratio. The accurate proportioning of these raw materials is essential to ensure that the reaction proceeds smoothly and that the final product meets the desired quality standards. Any deviation in the molar ratio can lead to incomplete reactions or lower product quality, making this step highly important.
Reaction in Autoclave
The mixture is placed in an autoclave, which is a high-pressure reactor equipped with an agitator to ensure uniform mixing throughout the process. The autoclave is specifically designed to withstand the high pressure and temperature required for the reaction. The temperature is maintained between 160°C and 200°C, while the pressure ranges from 0.6 to 1.5 MPa, creating optimal conditions for the chemical reaction. The agitation ensures that the reactants remain evenly distributed, preventing localized overheating or incomplete reactions. During the process, sodium hydroxide reacts with silica sand to form sodium silicate and water. The reaction is represented by the following chemical equation:
2NaOH+SiO2→Na2SiO3+H2O
The high temperature and pressure conditions help to break down the silica structure and facilitate its combination with sodium hydroxide, ensuring a high yield of sodium silicate.
Completion of Reaction
The reaction duration can vary from several hours to more than a day, depending on factors such as temperature, pressure, and the quality of raw materials. Maintaining these conditions within the specified range is crucial to ensure complete silica conversion into sodium silicate. Monitoring the reaction progress is essential, as incomplete conversion can lead to reduced product quality and yield. The prolonged reaction time allows for thorough interaction between silica and sodium hydroxide, ensuring that the final product is free from unreacted silica. This stage is vital for optimizing the yield and ensuring that the sodium silicate produced meets all required specifications.
Filtration and Concentration
After the reaction is complete, the mixture undergoes filtration to remove any unreacted silica particles or impurities. This filtration process is critical to ensure the purity of the final product, as any remaining solid particles can affect the quality and properties of sodium silicate. High-quality filtration equipment is used to separate these impurities effectively. If a higher concentration of sodium silicate is required, the solution can be subjected to an evaporation process. During evaporation, excess water is removed to achieve the desired density and concentration. This step must be carefully controlled to prevent crystallization or degradation of the product, ensuring that the sodium silicate remains in its optimal form for various applications.
Storage
The final sodium silicate solution is stored in tanks that are designed to prevent contamination and maintain product quality. These tanks are typically made from corrosion-resistant materials, ensuring that the sodium silicate remains stable during storage. The stored solution can be kept at controlled temperatures to maintain its desired viscosity and prevent any unwanted reactions. Once the product meets all quality standards, it is either used for further in-plant processing, such as blending or dilution, or distributed to customers in tanker trucks or containers, depending on the requirements of the end-user.
Quality Control and Specifications
The SiO₂/Na₂O ratio is a critical parameter that determines the properties and applications of the final product. Regular checks are performed to ensure purity by identifying any impurities, such as iron or aluminum. Additionally, properties like viscosity, density, pH, and appearance are monitored to meet production specifications.
Advantages and Disadvantages of the Wet Method
The wet process has several advantages, including lower energy consumption since it does not involve melting raw materials, direct production of the sodium silicate solution, and reduced carbon dioxide emissions, which makes it more environmentally friendly. However, it also has disadvantages, such as limited product variability due to specific SiO₂/Na₂O ratios and longer reaction times, which may extend production cycles.
Sodium Silicate Applications
Sodium silicate, also known as water glass, is a multipurpose compound used across many industries due to its unique properties, such as adhesive strength, alkalinity, and the ability to form a glass-like solid. Below is a detailed overview of the wide-ranging applications of sodium silicate.
Automotive Industry
Sodium silicate plays an important role in automotive maintenance, specifically as an engine sealant. It is introduced into the cooling system, where it forms a glass-like layer upon heating. This layer effectively seals cracks in engine blocks and head gaskets, helping to prevent coolant leaks and maintain proper engine function.
Manufacturing
Sodium silicate is utilized in various manufacturing processes:
- Silica Gel Production: It acts as a precursor in the production of silica gel, which is commonly used in moisture-absorbing packets for packaging and storage.
- Casting and Molding: Sodium silicate is used as a binder for sand molds in industrial casting processes. This provides strength and stability, allowing molten metals to be molded effectively without breaking down.
Wastewater Treatment
In wastewater treatment, sodium silicate functions as a flocculant, aiding in the removal of heavy metals and impurities. It promotes the coagulation process, which helps separate suspended solids from the liquid, improving the efficiency of wastewater purification.
Drilling and Soil Stabilization
Sodium silicate serves as a soil stabilizer during drilling operations. It reacts with the soil particles to create a solid mass, which prevents the collapse of loose or granular soils during excavation, thus improving stability in drilling environments.
Foundries and Ceramics
In foundries and ceramics, sodium silicate has two main applications:
- Ceramic Binder: It acts as an adhesive for bonding ceramic surfaces, contributing to the integrity of ceramic products during manufacturing.
- Deflocculant in Slip Preparation: Sodium silicate is added to ceramic slip to reduce viscosity, making the molding and shaping processes more manageable.
Textile Industry
Sodium silicate has specific uses in the textile industry, providing both fire retardant properties and insect protection. When applied to fabrics, it forms a heat-resistant barrier that provides passive fire protection. It is also used as a coating to protect textiles from insect infestations.
Adhesives
Sodium silicate is a common component in adhesive formulations:
- Paper and Cardboard: It is used in adhesives for paper products, including corrugated cardboard and shipping boxes, providing strong bonding that is crucial in packaging applications.
- Glass and Leather: Due to its strong bonding properties, it is also used as an adhesive for glass repair and in leather binding applications.
Detergents
In the production of laundry and dishwashing detergents, sodium silicate serves as an ingredient that enhances cleaning efficiency. It acts as a builder, softening water and aiding in the emulsification of oils and greases, which makes it effective in removing stains and improving overall detergent performance.
Food Preservation
Historically, sodium silicate has been used in the preservation of eggs. By coating the eggshells, it forms a seal that prevents bacteria from entering and slows down moisture loss, thereby extending the freshness of eggs for a longer period.
Concrete Applications
In the construction industry, sodium silicate is used in concrete applications:
- Concrete Sealer: It is applied to concrete surfaces to reduce porosity and improve durability. This helps protect concrete against water infiltration and chemical damage.
- Hardening Agent: Sodium silicate reacts with calcium hydroxide in concrete to form calcium silicate hydrate, which enhances surface hardness and extends the lifespan of the concrete.
Fire Protection
Sodium silicate is incorporated into fire-resistant materials to provide passive fire control. When exposed to high temperatures, it forms an insulating layer that helps limit the spread of fire, making it a valuable component in fire safety products and coatings.
About Nobel Trading Co’s Sodium Silicate Powder and Liquid
Nobel Trading Co, headquartered in China, is a trusted supplier of high-quality sodium silicate in both powder and liquid forms. As a major shareholder in specialized production facilities, the company is known for its commitment to delivering reliable products that meet diverse industrial demands. With strong connections to global mining sources, Nobel Trading Co efficiently secures raw materials to ensure competitive pricing and consistent supply.
Product Types: Sodium Silicate Powder and Liquid
Nobel Trading Co provides both powder and liquid grades of sodium silicate, each with distinct features and applications:
1. Powder Form
Sodium silicate powder is valued for its ease of handling and storage. This grade is particularly suitable for uses where a solid form is necessary, such as in the production of detergents and adhesives, or in construction applications like concrete hardening.
2. Liquid Form
The liquid grade of sodium silicate is appreciated for its adaptability. It is extensively used in industries like textiles, paper, and wastewater treatment. Its liquid nature allows it to blend readily with other substances, making it ideal for situations where quick reaction and high reactivity are essential.
Ensuring Quality: Production Facilities and Expertise
Nobel Trading Co’s advanced production facilities and skilled team ensure that all sodium silicate products meet high standards:
– Advanced Manufacturing Plants:
Equipped with cutting-edge technology, Nobel Trading Co’s factories adhere to strict quality control throughout the production process.
– Experienced Professionals:
The production team is composed of skilled professionals who ensure the product maintains high purity and consistency to meet industry standards.
– High Production Capacity:
With a substantial production capacity, Nobel Trading Co ensures reliable supply even for large-scale orders.
Affordable and Competitive Pricing
The company’s ability to provide competitive pricing stems from several key factors:
– Strong Mining Partnerships:
Nobel Trading Co’s established relationships with mines worldwide provide a steady supply of raw materials at favorable costs.
– Economies of Scale:
Ownership of multiple factories allows for cost-effective production, which results in more affordable pricing for customers.
– Streamlined Logistics:
Efficient supply chain and logistics management reduce operational expenses, contributing to competitive pricing.
Packaging and Shipping Solutions
Nobel Trading Co offers customized solutions to address the diverse needs of its clients:
- Customized Packaging Options
The company provides various packaging options, including moisture-resistant bags, drums, and bulk containers, ensuring that every customer’s specific needs are met.
- Multiple Shipping Methods
To ensure timely and safe delivery, Nobel Trading Co offers shipping by both sea and air freight, depending on customer preferences.
- Logistics Expertise
The logistics team at Nobel Trading Co handles every aspect of shipping, from necessary documentation to international compliance, to make sure that products reach customers smoothly and without delay.
Comprehensive Customer Support
Nobel Trading Co is committed to providing excellent customer service and support:
– Technical Support:
The company offers technical guidance to help customers make the best use of sodium silicate in their industrial processes.
– Quality Assurance:
All products are rigorously tested to ensure compliance with international standards. Nobel Trading Co also provides safety data sheets (SDS) and necessary certifications.
– Responsive Communication:
The company is dedicated to prompt communication, ensuring customer inquiries and issues are addressed efficiently.
Benefits of Choosing Nobel Trading Co
With a consistent track record of delivering high-quality products, Nobel Trading Co has established itself as a reliable supplier.
- Global Service Capabilities
Thanks to robust shipping and logistics systems, the company can effectively serve customers worldwide, regardless of their location.
- Customer-Focused Approach
Nobel Trading Co emphasizes building long-term relationships by fully understanding and fulfilling each client’s unique needs.